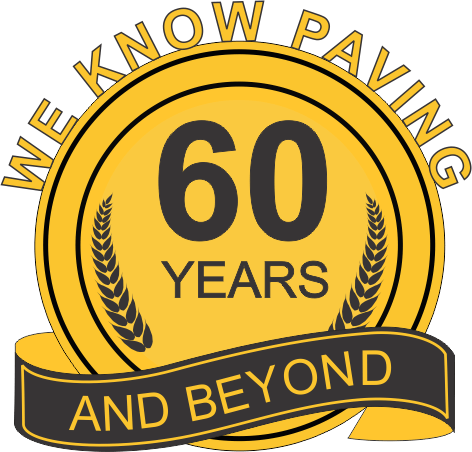
FREQUENTLY ASKED QUESTIONS
Concrete vs. Asphalt? What you need to know.
Actually, asphalt and concrete are both a type of “concrete”. Both materials are a mixture of sand, aggregates, special chemicals and cement. Asphalt, or Hot Mix Asphaltic Concrete (HMAC), uses asphaltic cement, a very thick material derived from the cracking process that yields petroleum fuels. Concrete, or Portland Cement Concrete (PCC) uses a cement, produced by heating limestone and clay minerals in a kiln to form clinker, grinding the clinker, and adding 2 to 3 percent of gypsum.
What is Recycled Asphalt Paving?
Asphalt Pavement Recycling, or Full-depth reclamation (FDR) rebuilds worn out asphalt pavements by recycling the existing roadway. The old asphalt and base materials are pulverized, mixed with cement and water, then compacted and graded to produce a strong, durable base for an asphalt surface. Full-depth reclamation uses the materials from the deteriorated asphalt pavement, and, with the addition of cement, creates a new stabilized base. The recycled base will be stronger, more uniform, and more moisture resistant than the original base, resulting in a long, low-maintenance life. And most important, recycling costs are normally at least 25 to 50 percent less than the removal and replacement of the old pavement.
Why is my pavement cracked? What does it mean? What can I do about it?
There are many factors that cause pavements to crack. Here in North Texas, the most common cause of pavement cracking, both asphalt and concrete, is ground movement. Our clay soils have the potential shrink and swell depending on the amount of moisture in the ground. Every summer, the ground dries and opens up large cracks. And as the ground cracks, often the paving place on top of the ground will crack. This is just part of living in the DFW area. These problems are best addresses with a proactive maintenance program of joint/crack sealing and monitoring the paving for potential failures.
More serious is the cracking that occurs with pavement failure. Even properly constructed pavement is subject to failure if the sub grade below it cannot support the traffic placed on the pavement. Whether the problem is sub grade failure or improperly constructed paving, it is best to remove the pavement, repair or replace the sub grade and place new paving in place of the old.
Concrete has unique situation related to the natural shrinkage of concrete as it cures and dries. Shrinkage concrete cracking can be controlled or hidden by following proper jointing techniques and maintenance through joint/crack filling.
Different factors and conditions can contribute to each type of cracking. It is important to understand these potential causes and take appropriate action to prevent cracking and the subsequent need for repairs.
More serious is the cracking that occurs with pavement failure. Even properly constructed pavement is subject to failure if the sub grade below it cannot support the traffic placed on the pavement. Whether the problem is sub grade failure or improperly constructed paving, it is best to remove the pavement, repair or replace the sub grade and place new paving in place of the old.
Concrete has unique situation related to the natural shrinkage of concrete as it cures and dries. Shrinkage concrete cracking can be controlled or hidden by following proper jointing techniques and maintenance through joint/crack filling.
Different factors and conditions can contribute to each type of cracking. It is important to understand these potential causes and take appropriate action to prevent cracking and the subsequent need for repairs.
Scuffing of New Asphalt Pavement - "Power Steering Marks"
Scuffing of a new asphalt surface is a completely normal and expected situation when summer temperatures are regularly above 90 degrees. The marks seen in the parking lot are usually caused by drivers turning their steering wheel while remaining in one place while trying to park. These scuff marks are cosmetic and, in most cases, will “selfheal” as future traffic re-rolls the asphalt.
We have found over our 60 years of installing asphalt that it is best to wait for temperatures to cool enough for the new asphalt to calm down and quit new scuffing.
We have found over our 60 years of installing asphalt that it is best to wait for temperatures to cool enough for the new asphalt to calm down and quit new scuffing.
Blacktop, Overlay, Sealcoat, Slurry seal. What’s in a name?
Generally, blacktop and overlay are interchangeable terms. They both refer to the application of an asphalt surface on top of existing paving, either asphalt or concrete. When discussing commercial work, sealcoat refers to the application of a coal tar or asphalt emulsion to asphalt paving. The materials slow the normal aging process of an asphalt surface. However, when used by County or State road departments in Texas, sealcoat refers to the “chip seal” process. Asphaltic cement is sprayed directly on existing paving or base material, then a thin layer of aggregate is spread and rolled with pneumatic rollers to force the aggregate and cement into a thin paving layer. To some in the paving industry, slurry seal is just another name for a sealcoat. To others, the term is used to describe a process similar to sealcoat, but the liquid material is mixed with enough small aggregate, sand, clay and other materials to produce an application of up to 1/4“ thick. Make sure you and your paving estimator are talking about the same process.
Maintenance of your parking lot.
We recommended that asphalt parking lots be maintained regularly to prevent surface aggregate from deteriorating, to slow the formation of stress cracks and also to maintain the aesthetics of your property. Annual inspection for crack-filling will allow you to stop water penetration before it can damage the paving sub base. Sealer should be applied to your lot at least every two to five years. Repairs will be necessary more often when excessive rutting, cracking or other structurally failed areas develop.